What happens when you cannot track or manage the time it takes to manufacture and package items before shipping them to customers?
Manufacturing procedures are seldom simple. Slow turnaround times might hurt your bottom line. Understanding your production processes and cycles is the most effective technique for reducing late output and turnaround time.
The manufacturing cycle is an integral component of all forms of manufacturing. In this article, we explain what the manufacturing cycle is and all you need to know about it to comprehend the manufacturing process
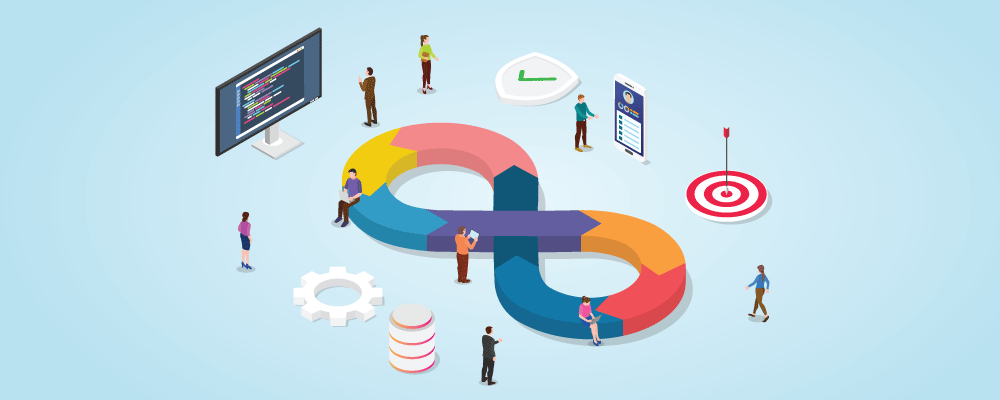
What is Manufacturing Cycle?
The manufacturing cycle is converting an idea into a working product. It is a process that starts with designing a new or existing product and finishes with assembling those pieces to create the completed product.
Manufacturing can be simple or elaborate. The primary difference is the process’s level of complexity and repetition.
For example, a simple manufacturing process varies from a complicated one because it requires only one flat bill of material for the project. Subassemblies will be employed in a complex manufacturing cycle to construct the product.
Whether your production cycle is simple or complex, it will go more smoothly if planned and managed with project management software.
Simplify project management
with nTask today!
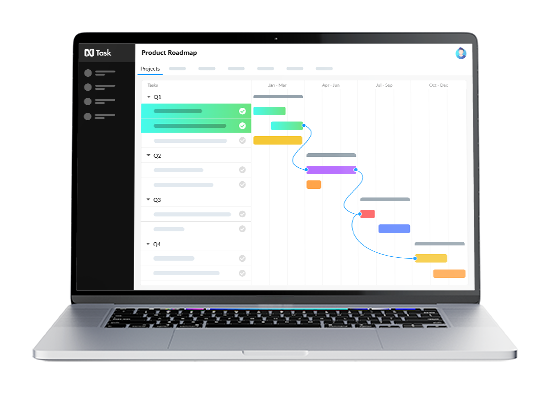
What are Manufacturing Projects?
Manufacturing projects, at their core, involve the creation of tangible goods from raw materials through various processes, transforming them into valuable products for customers.
In today’s highly competitive market, it is crucial to ensure that your manufacturing processes are efficient, well-coordinated, and innovative to stay ahead of the competition. That’s where manufacturing project management plays a vital role in the success of your business.
As a project manager, you’ll oversee the entire product manufacturing cycle – from conception to delivery. This encompasses collaborating with different departments and stakeholders, managing resources and schedules, and mitigating risks.
The primary objective is to deliver high-quality products within the given time and budget constraints while optimizing resource utilization and maximizing efficiency.
To succeed in managing a manufacturing project, you must have a comprehensive understanding of the manufacturing cycle. This includes the entire process, from procuring raw materials and designing the product to producing, assembling, and shipping the finished goods.
You’ll also need to be well-versed in manufacturing cycle efficiency, manufacturing process management, and manufacturing cycle time to effectively optimize the production process.
In addition, exceptional communication and leadership skills are essential for coordinating various teams, aligning goals, and ensuring that all parties are working in unison towards the project’s success.
Problem-solving and critical thinking abilities will also prove invaluable in addressing challenges and adapting to the ever-changing demands of the industry.
By mastering the intricacies of manufacturing project management, you can enhance your organization’s production capabilities, improve product quality, and ensure the timely delivery of goods to your customers.
Ultimately, this will lead to increased customer satisfaction, higher profitability, and a stronger competitive advantage in the market.
Embracing the principles of manufacturing project management will provide you with the necessary tools and skills to successfully navigate the complex world of manufacturing and achieve sustainable growth for your business.
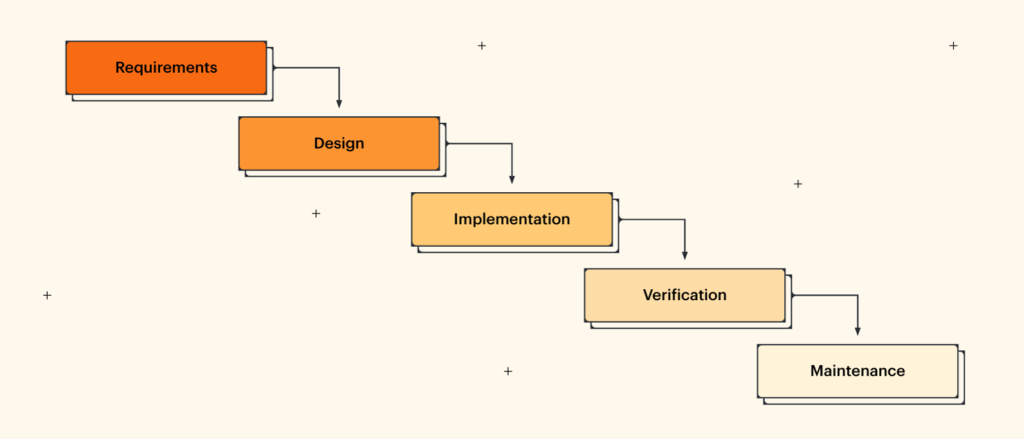
6 Essential Steps of the Manufacturing Cycle
If you have a new product concept, you have most likely given it thoughtful consideration, including the design, general utility, price, and market application.
It would help if you also thought about the process, particularly the product development and manufacturing.
You may be inclined to speed through some phases, but doing so is perilous.
Here is the 6-stage manufacturing process that you should employ.
1 – Product Design Planning
It is a long process that should not be hustled. There is far too much risk to take shorts or skip critical steps.
You probably have an idea or a sketch of what this product will look like, but resisting the impulse to dive in is vital.
In this method, the planning step is critical. It is your best bet for protecting your investment and producing a lucrative product that meets your expectations.
The Product Requirements Document (PRD), also known as the User Requirements Document (URS), is crucial to the planning phase and acts as a road map for the manufacturing process.
You will learn about product functionalities, performance demands, regulatory requirements, environmental concerns, and mechanical/electrical requirements by completing your PRD.
By the end of this phase, you must have a collection of high-level documents defining your PRD’s market demands and a timeframe and budget for the design project.
2 – Industrial Design
The industrial design team has received the specs for your product design.
Their willTherecks along the way (design reviews) to ensure the product fulfills the criteria while also allowing for PRD changes if more needs are discovered, either by the design team or through research on the technology or the client application.
Design Methodology
The outcome of the design process can take various forms. Still, the minimum design output must be a collection of documentation and design database information to produce a repeatable and reliable product.
The design process must also be controlled so that it is easy to check if the design output satisfies the design input and deals with any design issues that arise along the way.
A risk management approach must be included in the design process to detect and reduce any significant risks to product safety and function.
Design Control Procedure
The design control process comprises a series of checkpoints in a manufacturing cycle that must be performed at both major and minor design milestones.
Every design output should be assessed before it is released for manufacture. To put it another way, a design review is in order if you publish a paper, a schematic, a part drawing, a technique, or anything else.
Risk Management Procedure
Medical devices are subject to the risk management method. Sometimes the risks of a product are apparent, but you would be surprised. This is more than a series of FMEAs (Failure Mode and Effects Analysis), but it is a great place to start.
3 – Prototype
Building the initial prototypes is a critical aspect of the product development cycle since it represents the beginning of the manufacturing phase.
An Alpha Prototype is also known as a proof-of-concept model. Early in the design phase, it is aimed to evaluate the basic technologies on which the product is constructed. The need for one or more Alpha prototypes derives from considering the risks of moving forward.
A Beta Prototype is the prototype that is the entire product. It may lack packing, or the color may not be final, but it should be adequate for comparing the design to the design guidelines and the PRD.
In an ideal world, the design and materials are close enough to the final product design that any regulatory testing can be performed with little likelihood of changes when the product is given to manufacturing.
The manufacturing process is tested using pilot production.
4 – Design for Manufacturing
Your product will be modified during the Design for Manufacturing (DFM) stage to correct any defects detected during the prototype phase. The design and manufacturing procedures will be improved to improve manufacturability and reliability.
Now is the moment to scale it up, whether only a few units each month or a large order of thousands.
The design and prototype stages are usually the most fun parts of the project since you get to see what the final product will look like.
It is the only place where you can know if a product is in the works. However, the main business value is realized at the Design for Manufacturing (DFM) stage.
A prototype is not ready for large production on its own. Depending on the scenario, it is only one unit (or numerous), and the engineering team has thoroughly examined it at each level.
However, mechanisms must be put in place to manufacture at a production level to allow it to be built efficiently, often, and without engineers.
Design for manufacturing is also in charge of the necessary paperwork, which includes anything from assembly instructions to test protocols.
5 – Manufacturing
Your product is now complete and ready for assembly and production.
You have taken every measure to guarantee that the manufacturing process runs smoothly and efficiently.
A significant investment in space, equipment, and personnel is necessary to generate a repeatable and dependable product.
With a simple product and a limited number of clients, this may work for a time.
There are several aspects to consider while deciding how to design your product.
6 – Post Manufacturing
Your business is up and running, and finished items are being delivered to customers.
So, what happens next? How will your items be distributed, deployed, and maintained? Who is going to teach the user how to use the product?
At this stage, your primary focus should be on customer service, which includes providing the user with everything they need to enjoy your product effectively.
Depending on the product, this may include a field service specialist for installation, setup, commissioning, maintenance, repair depot, and manufacturing training for your service personnel.
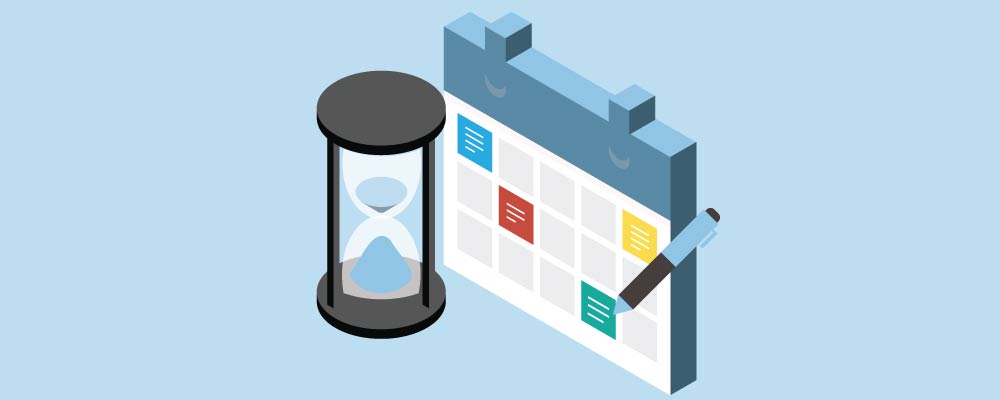
Benefits of Manufacturing Project Management
Effective manufacturing project management offers a range of benefits that can help you streamline your processes and stay competitive in the industry. Some of these benefits include:
Improved efficiency: By closely managing the manufacturing cycle, you can identify bottlenecks, eliminate waste, and optimize your operations. This can lead to shorter cycle times and better overall efficiency. Implementing lean manufacturing principles and continuous improvement initiatives can also contribute to enhanced productivity and reduced downtime.
Enhanced product quality: Manufacturing project management helps you maintain a strong focus on quality control. By monitoring production closely and addressing issues as they arise, you can ensure the end product meets or exceeds customer expectations. This also helps in minimizing defects, reducing rework, and lowering the likelihood of product recalls.
Increased cost savings: Effective project management enables you to better control costs through proper resource allocation, waste reduction, and improved decision-making. It also allows for more accurate cost estimates, budgeting, and forecasting, which ultimately leads to better financial performance for your organization.
Timely delivery: Manufacturing project management helps you meet customer deadlines and maintain a positive brand reputation. By closely monitoring the progress of your project, you can anticipate and address any potential delays. This ensures that you can deliver your products on time and meet your customers’ expectations.
Better collaboration: Project management encourages communication and collaboration between various teams and departments, helping you work together more effectively and efficiently. This leads to improved information sharing, faster problem-solving, and a more cohesive and aligned organization.
Increased flexibility and adaptability: Manufacturing project management allows you to quickly respond to changing market demands, customer preferences, and technological advancements. By staying agile and adaptable, you can maintain a competitive edge and capitalize on new opportunities as they arise.
Greater visibility and control: Implementing manufacturing project management practices provide you with better visibility into the status of your projects, resources, and overall performance. This increased transparency enables you to make more informed decisions, identify potential issues early on, and effectively allocate resources to address them.
Enhanced risk management: A comprehensive project management approach helps you identify, assess, and mitigate risks associated with your manufacturing projects. By proactively addressing potential challenges, you can minimize disruptions and ensure the success of your project.
What is the Manufacturing Cycle Time?
Manufacturing cycle time is an essential metric for manufacturers. It denotes the time spent on an item from raw material to finished product.
Cycle time includes an item’s processing, movement, inspection, and waiting time – it consists of the whole process, including the idle time a product spends moving through the manufacturing facility.
Another method for determining production cycle time is to divide the total number of products by the net production time.
Process Time
This is the time it takes to transform raw materials into finished goods. Product redesign can shorten the processing time.
Change processing Time
This is the time it takes to move an order from one workstation to another. It may be compressed by putting workstations closer together and moving items continuously via conveyors.
Period of Inspection
This is the time required to check a product to ensure defect-free. Inspections can be integrated into the production process, eliminating the need for a separate inspection function.
The formula for cycle time
We may derive our formula from the description of how to compute cycle time in manufacturing as follows:
Net production time = Cycle time (per product)
However, the calculation above may appear to be overly tricky. Consider the following simple formula:
Non-productive hours multiplied by productive hours (per product) equals cycle time.
or
Cycle time = Process time + Inspection time + Movement time + Queue time (per product)
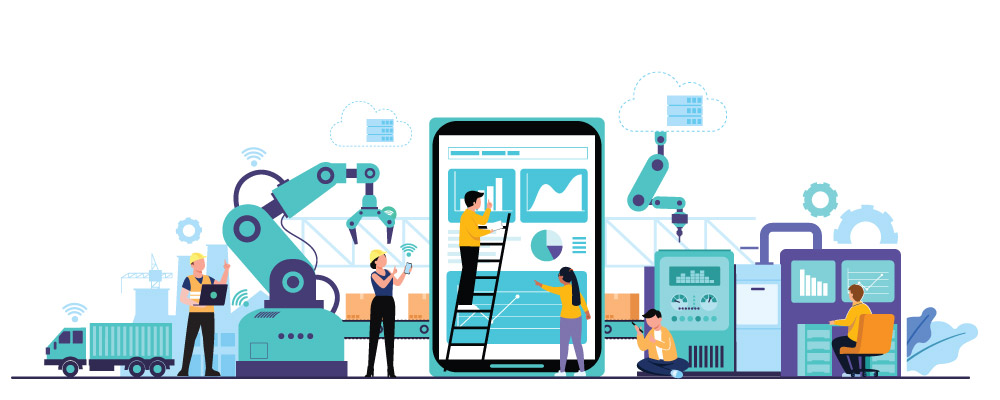
Why Should You Monitor the Manufacturing Cycle?
Estimating and tracking production cycle time can have significant financial consequences. A corporation can boost productivity, focus on capacity consolidation, and reduce yield/loss or logistical challenges by shortening the manufacturing cycle time.
Knowing the cycle time may help businesses improve their lean manufacturing by signaling to teams what goal to set to order to produce a product.
The shorter the manufacturing cycle time, the better for the firm, as long as product quality is not compromised.
Other advantages of computing cycle time include the following:
1. Enhanced profitability
Calculating cycle time helps you identify where most of your time is spent in production, so you can cut back on time and enhance profit.
2. Consistent output rates
Cycle time assists firms in understanding their production flow to reduce waste efficiency.
3. Client satisfaction
Customers must be given realistic product development timetables. Cycle time tracking assists in determining the exact delivery duration that clients may rely on.
4. Create a competitive advantage
Cycle time helps firms keep ahead of the competition by giving real-time information on a delivery time range. Business owners that work at a snail’s pace might reduce production time and gain a competitive advantage.
5. Extensive data on corporate expenditures
Individually funded operations should provide value to your manufacturing process, but some don’t. Business owners, manufacturers, and product managers may better understand expenditure management and enhance efficiency by measuring cycle time. In summary, cycle time helps you better understand your business operations.
How to Improve Manufacturing Cycle Efficiency?
Improving the efficiency of your manufacturing cycle entails much more than implementing a lean manufacturing strategy that focuses just on the manufacturing process.
To accomplish cycle time optimization, it is required to examine all parts of the production cycle, from order placement to the manufactured product landing in the hands of the consumer.
Many organizations focus on manufacturing methods, not realizing that waste and inefficiency may have already been integrated into the product.
Manufacturing cycle efficiency begins before the product is manufactured and continues after the product has left the shop floor.
Production Cycle Efficiency refers to the proportion of manufacturing time spent on value-added activities. Manufacturers can save costs by identifying jobs that add no value to the process.
Evaluating manufacturing cycle efficiency is essential because it helps you better understand what percentage of cycle time is made up of value-added processes. This data is frequently surprising since manufacturers only monitor a small fraction of the whole cycle time that is effective.
FAQs
What is project-based manufacturing?
What is the basic manufacturing process?
What is the formula to calculate manufacturing cycle time?
Manufacturing Cycle Time = Process Time + Inspection Time + Move Time + Queue Time
This formula takes into account the time spent on each stage of the manufacturing process, as well as any delays or waiting periods that may occur between stages. By analyzing and optimizing each component of the cycle time, you can improve efficiency and reduce the overall time it takes to produce a finished product.
Wrapping it up
Nobody wants to lose loyal customers or risk costly downtime due to over-commitment and poor production.
Understanding your manufacturing processes and cycle time, on the other hand, aids in the prevention of discrepancies while also ensuring efficiency and productivity.
Cycle time is a crucial indication that enhances how your business runs while increasing profitability, quality items, and consumer retention, whether you utilize it for a large or small-scale organization.