PDCA cycle is a four-step cycle for constant improvement. Companies constantly evolve to keep up with the rapidly advancing world. PDCA approach is one way to inducing these changes in the system.
PDCA cycle is the means to making sure that your company is constantly improving and is headed in the right direction. In terms of marketing, for example, businesses have transitioned from country-wide print media ads to strong social media campaigns targeting audiences across the globe.
Similarly, adopting changes in management is a much-needed constant process. Enter PDCA cycle.
Perfecting a project requires a lot of hard work, timely management, and frequent evaluations. Besides these pointers, a company also needs to keep up with the latest trends in the market. That means it has to regularly introduce new changes in its system.
Stagnancy lowers down a company’s chances to move ahead and hinders its progress. This is where improvements come in handy. Carefully planned processes of inducting improvements make it easy for companies to make their way to the top.
That being said, transitioning into new changes and adapting them requires keen observation and impeccable strategizing. This is where the PDCA model approach proves to be really helpful.
What Is The History Of PDCA Methodology?
Before we explain the PDCA cycle, let us look into its history. The idea was founded by American physicist Walter e. Shewhart in the 1920s. The idea aimed to improve quality through frequent evaluations.
The cycle was, later, developed and popularized by an American professor, William Deming. Deming, considered the father of quality control, developed the cycle based on the scientific method of problem-solving.
We will now explain the PDCA cycle: its meaning and the purpose of the plan do check cycle.
What Is The PDCA Cycle?
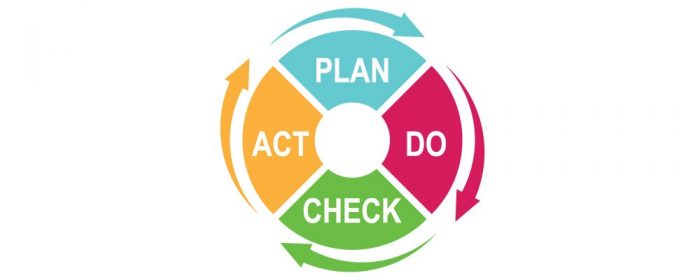
PDCA cycle is the abbreviation of plan-do-check-act. The methodology is a four-step cycle formerly named the Deming cycle.
The PDCA methodology aims to improve processes occurring in a company and help eliminate recurring mistakes. It is a project planning tool and is a key element of lean management.
Following the PDCA approach, companies should, first, plan a change that is to be adopted into the system. The second step involves the implementation of the plan. The effect of the change should, then, be checked in the next step and finally, act accordingly i.e. Keeping the results in mind, and continue or discontinuing the use of that change.
Be mindful of the fact that this is a cycle meaning the completion of each cycle prompts the initiation of the next one. In this way, companies remain in the loop of change and constantly evolve.
When Should The PDCA Be Used?
PDCA cycle has multiple uses, you can use it when:
- Evaluating multiple solutions
- Initiating a new improvement project
- Developing an improved design, process, etc.
- Implementing a new change
- Improving a process
- Continuously improving
The best thing about this cycle is that it is applicable across multiple industries and various departments within the same company.
Let us now take a closer look at the ins and outs of the cycle and what it entails and how to use the PDCA cycle.
A Closer Look At The Plan-Do-Check-Act (PDCA) Cycle Model

The Plan-do-check cycle is an important component of Lean management where constant improvements are a given. The methodology helps companies plan for the future, analyze the results, and make important decisions regarding future developments in the company.
Let us explain the PDCA cycle and how to use the PDCA cycle by analyzing the 4 steps included in the cycle.
1. Plan
The first step in the cycle involves thorough planning and strategizing. In this stage, you plan all the steps to be taken in the future. The step starts by identifying the problem and developing a path to resolve the problem.
Planning is further divided into four smaller steps:
- Identify the problem
- Analyze the details of the problem
- Evaluate the root cause of the problem
- Devise an action plan
Some question that you need to answer in this stage include the following:
- What is the problem?
- What is the root cause of the problem?
- How can it be solved?
- What resources are needed to solve this problem?
- What resources do we have?
- What is the optimum solution for the problem?
- How will the solution impact the problem?
You must devise an impeccable plan so that the rest of the process has a smooth flow. You and your team might have to spend a lot of time and effort on this phase of the process. But it will be worthwhile since the impeccability of this step is a prerequisite for the success of the later stages.
2. Do
After you have thoroughly designed the action plan, it is time to implement the plan. this is the phase where you execute the plan you made previously.
Keep in mind that the execution may not be ideal since the processes are always susceptible to errors, but you can minimize those errors by strategizing your plan following all the possible hindrances.
This stage is the most important in the plan-do-check cycle so make sure to map all the changes and chart them accordingly. It is advisable to implement the plan in smaller steps in a controlled environment, this way you can minimize risks by evaluating results and planning accordingly so that the rest of the process is not affected.
3. Check
Once you have implemented the plan, you can now evaluate the results it produced. This stage is important because it allows you to review your plan, analyze its pros and cons, and make relevant changes wherever necessary.
You can check the results against the standard checklist developed in the planning phase or analyze them separately. If the outcome does not satisfy the hypothesized progress then you can look for better solutions.
You also need to identify problems or if something went wrong during the process, you can, then analyze this problem and take measures in the planning phase to eliminate the risk in the future.
Since this step will guide your decisions, make sure that all the results are duly charted and there are no loopholes in the process.
4. Act
The final stage in the PDCA cycle is the act. This is the phase where you can iterate your plan based on the outcomes.
If your plan managed to fulfill all the requirements and has produced fruitful results then you can implement the plan on a larger scale. Your plan will now, become a standard, but, make sure to follow all the steps and make amendments wherever necessary to avoid any fallouts.
In case your plan failed to achieve the proposed results, you can move back to the first step and plan the project again. Don’t worry your experience will add to your expertise and the next plan you make will be even more effective than the previous one.
With the PDCA cycle not only can you plan and introduce new changes in your management but can also improve the existing processes to make them even better.
Kanban Boards in PDCA Cycle
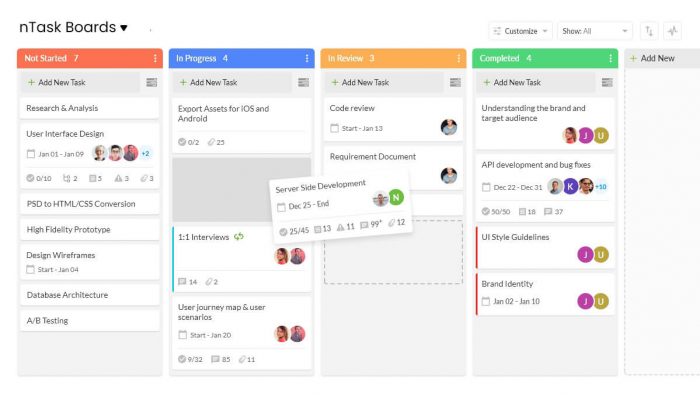
To make your life simpler and easier, you can use Kanban boards for the PDCA approach. Using Kanban boards will make it easier for you to keep track of everything taking place in the process.
With the added advantage of visualization, you will be able to not only identify problems, track the latest developments in the project but will also be able to plan strategies to resolve the problems. There are various project management software that offers Kanban boards as an agile methodology for project management.
One of the best among these is nTask’s Kanban boards. You can utilize various perks of nTask’s Kanban boards including the following:
- Link projects
- Assign tasks
- Track time
- Personalize workflow
- Add status columns
- Customize the color of each status
- Choose your own initial and final stage
- Readymade templates
Along with these features, you can have the added advantage of real-time communication with your team members.
To use the Kanban board for the PDCA approach, you can create four columns titled plan-do-check-act. Using these four columns you can create tasks for your team members in each phase. The completion of tasks will move the project forward from one stage to the next one.
You will not only be able to keep an eye on the progress of your project but will also be able to identify bottlenecks or possible issues that may hinder the success of the process. You can, then, take appropriate measures and improve your plan.
(Plan-Do-Check-Act) PDCA in Project Management
In project management, it is necessary to follow the PDCA model to streamline planning and project efficiency in completing work on time with quality delivery. You can make use of project management tools like nTask to make use of the PDCA cycle approach in project management.
In order to finish projects on time, catering to all the requirements, and working with full efficiency requires implementing the PDCA methodology in your work processes, and making sure it is used across all the departments. Applying this concept in project management is a good PDCA example for project managers.
Conclusion
PDCA methodology can help your team solve problems and design changes to improve the overall productivity of the processes taking place in your company.
This methodology is easy to manage and can be used for multiple processes across different businesses to enhance your efficiency.
You can take the help of nTask’s Kanban boards for your PDCA cycle. You can keep your team members on the same page and visualize the whole process. This way you will have no problem executing your plan and observing the results.
nTask’s Kanban boards will be your gateway to success.
Happy nTasking!